YH auto R&D Direction
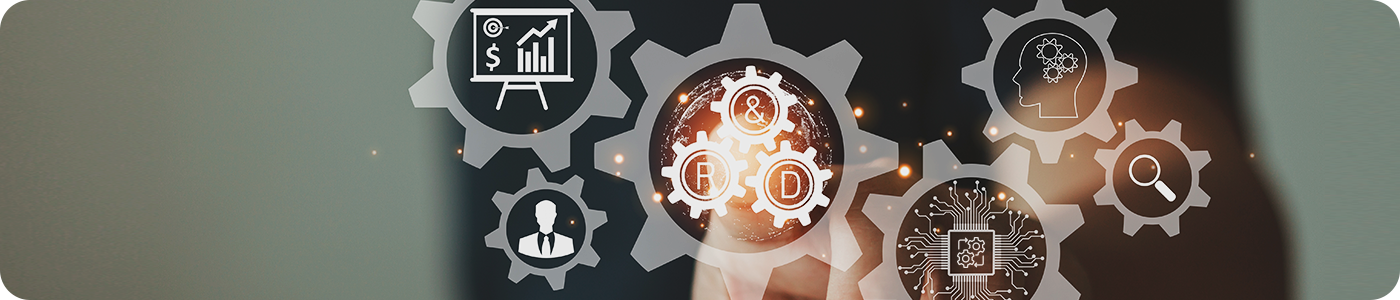
New Spring
Coil springs used in passenger car suspension systems are changing from the existing cylindrical regular shape to an irregular structure such as a pigtail type at both ends or a lateral force reduction type. Through design optimization, we are improving the lifespan of the suspension system and contributing to improving the fuel efficiency of automobiles by reducing the weight of springs by homogenizing stress and applying high-stress materials. The leaf spring used in the suspension system of large commercial vehicles such as trucks and buses has been changed from the current multi-plate structure to a parabolic structure to ensure weight reduction. To prevent joints due to slip in the multi-plate structure, the end silencer was changed to a rubber material to ensure noise prevention performance.
New Material
The tensile strength can be improved by optimizing the heat treatment process of the silicon-chrome steel (SAE9254) used as the spring material, and by applying it to coil springs, durability performance and weight reduction can be achieved. Recently, we are conducting research to improve coil spring performance by developing new materials that are robust in the corrosive environment caused by the use of snow removers in winter and have additionally improved tensile strength.
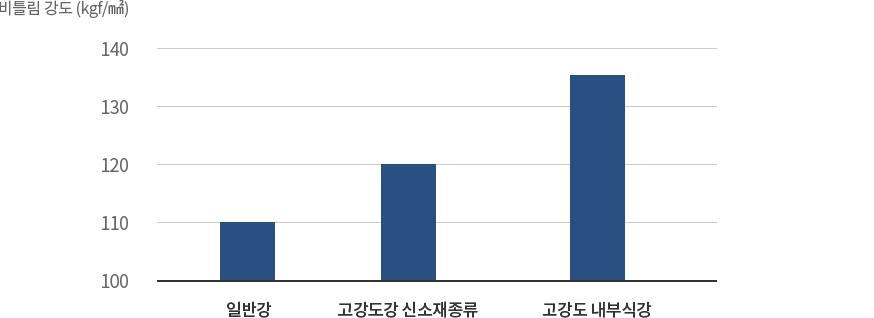
New Opportunity
As a compression coil spring material for automobile suspension, we developed a spring that can achieve a weight reduction of more than 5% even with the same material by applying a circular cross section to a different cross section (oval, cylindrical, etc.). In addition, we studied materials and springs that can achieve weight reduction of more than 20% by applying existing solid cross-section materials as pipe cross-section materials. Recently, research is being conducted to use glass fiber reinforced plastics (GFRP) instead of steel as a spring material to achieve a higher weight reduction ratio.